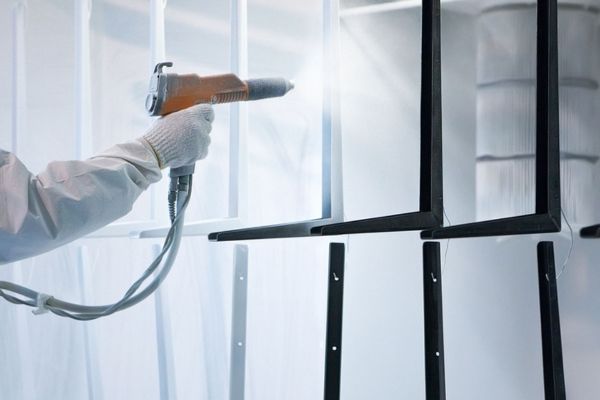
The Role of Powder Coating in Aerospace Applications
The aerospace industry operates in a demanding environment, where components are consistently exposed to extreme conditions. From high temperatures and harsh chemicals to constant wear and tear, the materials used in aircraft and spacecraft require exceptional durability and performance. This is where powder coating excels, offering a versatile and reliable solution for a wide range of aerospace applications.
At Crest Coating, we work with some of the top aerospace companies in the world including, Lockheed Martin, Northrop Grumman, SpaceX, Lisi, Honeywell, Collins, Adams Rite, and more.
What is Powder Coating?
Powder coating is a dry finishing process that involves applying finely ground polymer particles to a metal surface. These particles are electrostatically charged and adhere to the metal, creating a uniform and durable coating. Unlike traditional liquid paint, powder coating requires no solvents, resulting in a more environmentally friendly process.
Why Airplanes Need Coating
Aircraft are complex machines with thousands of moving and static parts, each requiring protection to ensure safe and efficient operation. Coating plays a multifaceted role in maintaining an aircraft’s performance:
- Lubrication: Proper coating reduces friction between moving parts, preventing wear and galling. This is essential for maintaining the functionality of high-friction components like landing gear and wing flaps.
- Corrosion Protection: Aircraft parts are exposed to harsh environmental conditions, including varying temperatures, moisture, and pollutants. Coating provides a barrier against oxidation and corrosion, significantly extending the lifespan of critical components.
- Efficiency: Coating helps reduce drag by creating smoother surfaces, aiding in improving aerodynamics. This reduction in drag translates to better fuel efficiency and higher speeds, which are crucial for long-distance travel.
Given these roles, it’s evident that coatings are essential in aircraft design and upkeep.
Advantages of Powder Coating in Aerospace
Powder coating offers several advantages for the aerospace industry, including:
- Thicker and More Durable Finish: Powder coating produces a thicker and more uniform coating than traditional liquid paints. This robustness is particularly beneficial for aerospace components that endure significant mechanical stress and exposure to elements.
- Environmental Friendliness: Unlike many conventional coatings that release volatile organic compounds (VOCs) during application, powder coating emits little pollutants. This characteristic makes it an environmentally responsible choice, aligning with the aerospace industry’s efforts to minimize ecological impact.
- Superior Adhesion and Coverage: The electrostatic application process ensures that powder coating adheres exceptionally well to surfaces, including complex shapes and hard-to-reach areas. This results in comprehensive coverage, leaving no part unprotected.
- Cost-Effectiveness: Over time, the durability and longevity of powder-coated finishes reduce the need for frequent reapplication, leading to cost savings in maintenance and materials.
Aircraft parts and structures require coatings that can withstand high-altitude conditions, temperature fluctuations, and exposure to fuels and fluids. Powder coating excels in these areas, offering high-quality resistance to corrosion and abrasion while maintaining the aesthetic appeal of aerospace equipment.
Applications of Powder Coating in Aerospace
Powder coating plays a crucial role in various aerospace applications, including:
- Exterior Surfaces: The exterior surfaces of aircraft, including fuselages and wing structures, benefit from powder coating’s robust protection. This coating resists chipping, scratching, and corrosion, ensuring the aircraft remains aerodynamically efficient and visually appealing.
- Interior Components: Inside the aircraft, powder coating is used on various components such as seat frames, overhead bins, and galleys. The finish not only protects these parts from wear and tear but also meets stringent fire safety standards.
- Landing Gear and Engine Parts: These critical components face intense stress and harsh environmental conditions. Powder coating provides the necessary durability and resistance to chemical and physical damage, ensuring these parts function reliably.
Environmental and Regulatory Compliance
The aerospace industry is heavily regulated, particularly concerning environmental impact. Powder coating’s minimal VOC emissions make it a preferred choice for meeting these regulations. By adopting powder coating, aerospace manufacturers demonstrate their commitment to sustainability and compliance with global environmental standards, contributing to a greener and more environmentally responsible industry. This commitment emphasizes the industry’s role in fostering a healthier planet for future generations.
Conclusion
Powder coating is more than just a protective layer for aircraft components—it is a crucial factor in enhancing performance, safety, and environmental responsibility in the aerospace industry. As aircraft continue to evolve with advancements in technology and design, the role of powder coating will only become increasingly significant.
Crest Coating is proud to contribute to this progress by providing top-quality powder coating services tailored to the specific needs of the aerospace sector. Our expertise ensures that every component we treat not only meets but exceeds the rigorous standards of the industry, helping aircraft fly safer, faster, and more efficiently. In an industry characterized by constant evolution, we remain at the forefront by staying abreast of the latest advancements in coating products, equipment, and application techniques.