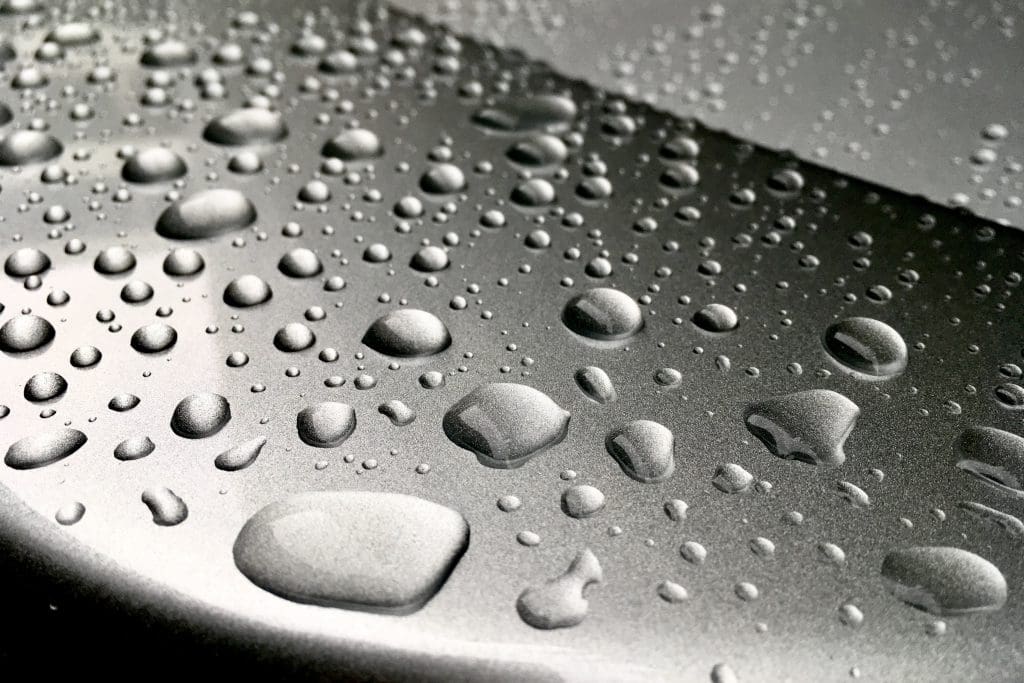
How Temperature and Humidity Affect the Powder Coating Process
Powder coating is a popular finishing technique known for its durability, efficiency, and eco-friendliness. However, the quality of a powder-coated finish is about more than just the coating itself. It’s also about the environment in which it’s applied. Temperature and humidity are the two key factors that play a major role in how well the powder adheres, flows, and cures.
Understanding how these environmental conditions impact the powder coating process is essential for ensuring a smooth, long-lasting finish. In this article, we’ll break down how temperature and humidity influence powder coating and share best practices to control these factors for optimal results.
Understanding the Powder Coating Process
Unlike traditional liquid painting, powder coating involves applying a dry powdered polymer to a surface using an electrostatic charge. The powder is then baked in an oven to cure, melting into a solid, durable coating. This process is widely used for industrial applications because it provides a tough, long-lasting finish that resists corrosion, chipping, and fading.
Since powder coating relies on precise application and curing, certain environmental factors like temperature and humidity must be carefully controlled to avoid defects such as uneven coverage, poor adhesion, or weak durability.
The Role of Temperature in Powder Coating
1. Powder Flow and Consistency
Temperature has a direct impact on how well the powder flows and adheres to the surface. The ideal ambient temperature for powder coating is between 65°F and 80°F. If the temperature is outside this range, several issues can arise:
- Too Hot: Powder can become too thick, causing defects like orange peel texture, pinholes, or excessive flow.
- Too Cold: The powder may not flow properly through the equipment, leading to clogging, uneven coverage, and a rough finish.
2. Impact on Equipment
Temperature also affects the functionality of the spray gun and other coating equipment:
- Cold temperatures can cause powder blockages in the spray gun, leading to inconsistent application.
- High temperatures can interfere with the electrostatic charge, reducing the powder’s ability to properly adhere to the surface.
3. Curing and Final Finish
Once applied, powder-coated objects are placed in a curing oven to bond the powder to the surface. This step is crucial, and temperature fluctuations can cause:
- Under-curing, leading to a weak, easily chipped finish.
- Over-curing, which can cause discoloration or a brittle texture.
While curing ovens have their own temperature controls, ambient temperature can still affect pre-heating and cooling rates, which would impact the final result.
The Role of Humidity in Powder Coating
1. Powder Adhesion Issues
Humidity levels greatly affect how well the powder sticks to the surface. The recommended humidity range for powder coating is 40% to 60%. If humidity is too high or too low, adhesion problems can occur:
- High Humidity: Powder particles absorb moisture, causing clumping, uneven application, and a blotchy finish.
- Low Humidity: The powder can become too dry, making it difficult to adhere evenly, leading to weak coverage and inconsistent texture.
2. Electrostatic Charge Performance
Since powder coating relies on electrostatic charge for adhesion, humidity plays a crucial role in how well the powder sticks:
- Too much moisture in the air disrupts the charge, making it harder for powder to adhere.
- Too little moisture can cause excessive static buildup, leading to powder repelling from the surface rather than sticking properly.
Best Practices for Controlling Temperature and Humidity
Maintaining the right environmental conditions is key to a successful powder coating application. Here are some effective ways to regulate temperature and humidity in your workspace:
1. Keep Temperature Within the Ideal Range
- Maintain workshop temperatures between 65°F and 80°F for consistent powder flow and application.
- Use HVAC systems or climate control units to regulate temperature changes.
- Store powder materials in temperature-controlled areas to prevent degradation.
2. Control Humidity Levels
- Use dehumidifiers or humidifiers to maintain 40%-60% humidity in the workspace.
- Store powder materials in airtight containers to prevent moisture absorption.
- Avoid applying powder coating in extreme weather conditions, especially in open or poorly ventilated areas.
3. Invest in High-Quality Equipment
- Choose powder spray guns with built-in environmental control features for better performance.
- Regularly maintain and clean equipment to prevent clogs and inconsistent powder flow.
- Consider air make-up units (AMUs) in enclosed spaces to maintain consistent temperature and humidity.
4. Conduct Regular Testing and Adjustments
- Perform test runs before full-scale powder coating to check for environmental issues.
- Adjust curing oven settings to compensate for ambient temperature fluctuations.
- Use humidity sensors and thermometers to continuously monitor conditions and make necessary adjustments.
Wrapping Up
Temperature and humidity are two of the most critical factors in achieving a high-quality powder-coated finish. By keeping temperatures between 65-80°F and humidity within 40-60%, manufacturers can avoid common defects, improve adhesion, and ensure durable, professional results.
For companies like Crest Coating, maintaining a stable coating environment is about ensuring efficiency, consistency, and cost-effectiveness.