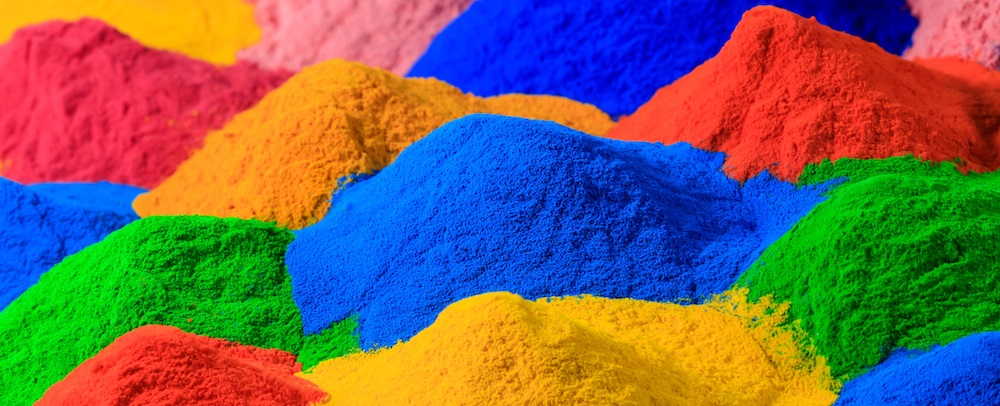
Pretreatment Is Key to Long-Lasting Corrosion Resistant Powder Coatings
Resisting shortcuts also lengthens the life of decorative impact.
There are many powder coatings that provide long-lasting, protective, corrosion-resistant surfaces. Powder coatings can be both decorative and corrosion-resistant for specific environments, but most important for the durability of the coating over the long term is the thoroughness of the pretreatment phase.
The most popular corrosion-resistant decorative powder coatings fall into a few categories based on their base formulas: epoxies, polyesters, epoxy-polyester hybrids, and fluoropolymers. Each of these can maximize corrosion resistance—and long-term durability—if you understand their strengths and apply them with the end-use in mind.
The thing is, powder coatings always look great when they’re new. But when that new finish doesn’t last as long as expected, or when it doesn’t provide corrosion resistance as expected, how do you know what the cause is? You don’t always know, because the answer is hidden. More often than not, the coating begins to fail because someone took a shortcut during the pretreatment phase.
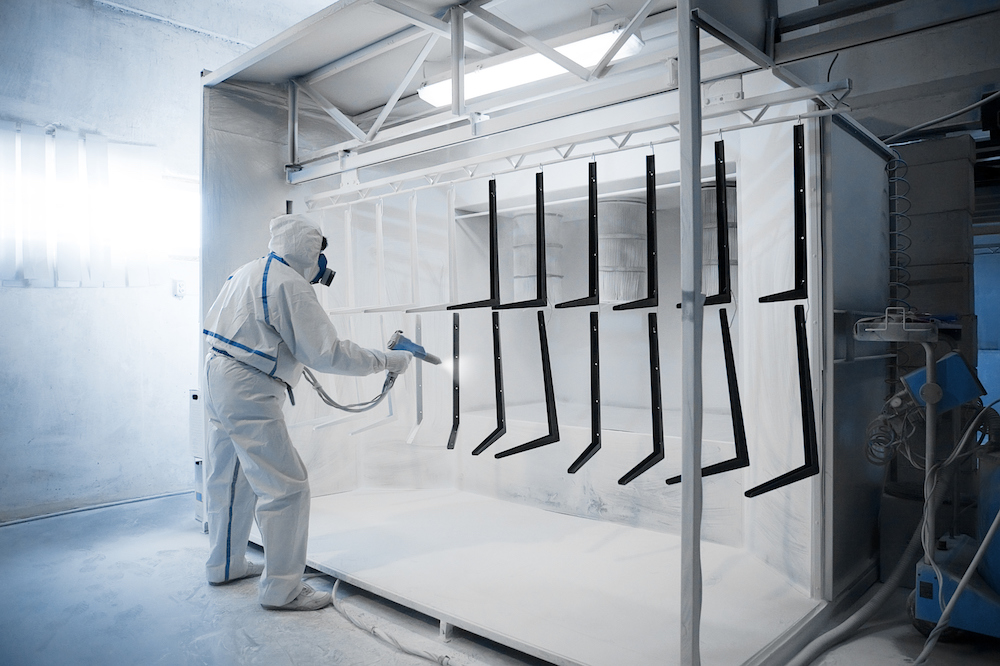
Thorough Pretreatments
Substrate preparation and pretreatment for powder coating is as important as—or more important than—the coating itself when it comes to corrosion resistance. Pretreatment is essential to ensure both product longevity and outstanding appearance.
When we talk about pretreatment, we usually mean sandblasting, a chemical conversion treatment, or both. Sandblasting can be done with aluminum oxide, steel shot, or garnet. There are lots of chemical conversion treatments out there, but we use zirconium, iron phosphate, and zinc phosphate. For long-lasting corrosion resistance, we recommend our in-house, six-stage zinc phosphate process for all ferrous substrates and our six-stage zirconium process for all non-ferrous substrates.
There are many ways to cut corners on pretreatments. These include shortening the pretreatment time, not staying within the recommended temperature range, failing to maintain chemical titration, failing to adjust pH, and not maintaining your water purity.
At Crest Coating, our emphasis is always on producing the highest quality finishes possible. We use the latest in electronic measuring and monitoring equipment, in-house RO and DI water systems, and quality control that complies with ISO9001:AS9100 standards.